Applications
History of Investment Casting
Precision casting is commercially known as Investment casting or lost wax casting.
Precision casting is the most ancient of metal casting arts, at the same time also the most modern and versatile. This process has been known and used for centuries. The history of 'lost wax' process goes back in time beyond the Egyptian pyramids. Artisans of Shang dynasty in China (766 - 1122) created art works of bronze into delicate filigree. Historians have lost track of the Precision Casting in Europe and Asia until the 16th century. but half way round the world in Cauca valley in Columbus. The remarkable statue "Shiva, Lord of Dance" was produced during the 8th and 9th century in India.
During the 16th century, the process was widely applied by artists and sculptors. Benvenuto Cellini produced many sculptures by this process. The most outstanding is the bronze statue of the Perseus with the Head of Medusa.
The "lost wax process" was also adapted by dentist during the late 19th century to produce accurate castings for filling crowns, bridges etc., often in gold. The continued development of the process during the early years of the 20th century laid the foundation of the engineering process as it is known today.
Investment Casting Production Process
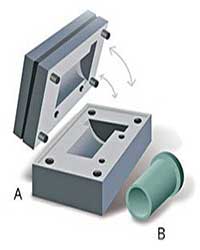
A wax injection die or mold is made which is the exact negative replica of the part to be made. This contains pull out cores which form slots, holes etc.
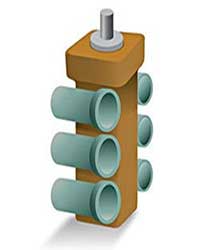
The wax patterns are assembled onto the sprue. The patterns are attached to a central wax stick, called a Runner, to form an assembly. Patterns used in sand casting may be made of wood, metal, plastics or other materials.
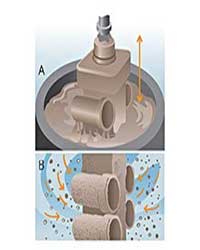
Successive layers of ceramic (A) and stucco (B) are applied to the sprue assembly to form a hard shell. The shell is built by dipping the assembly in a liquid ceramic slurry and then into a bed of extremely fine sand. Up to eight layers may be applied in this manner.
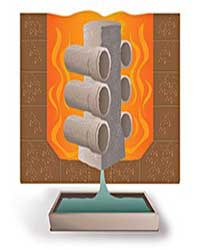
The molds are flash-fired to remove the wax and sprue materials and then heated to 1,800° and placed on a sand bed, ready for pouring. Dewaxing lubrication oil represents the largest use of scraped surface continuous crystallizers.
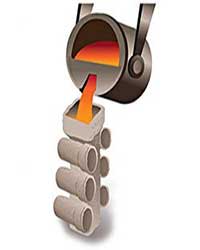
The shell is filled with molten metal by gravity pouring. As the metal cools, the parts, gates and pouring cup become one solid casting. Once the ceramic material is hardened its internal geometry takes the shape of the casting. The wax is melted out and molten metal is poured into the cavity where the wax pattern was.
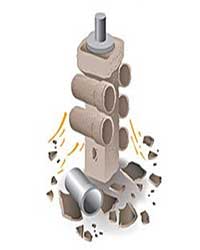
The ceramic shell is broken by vibration and the individual castings are cut away.
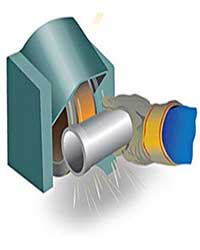
Excess metal is removed, surfaces are finished, and castings are heat treated. Traditionally, the parts are cut away from the central runner using a high speed friction saw, arc cutting, cutting disc or gas cutting. As cast surface finish can be provided by undertaking various post cast finishing processes.
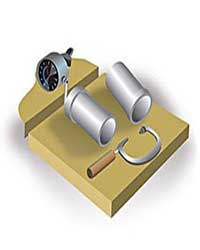
Castings undergo thorough testing and inspection to ensure that they meet dimensional tolerances and specifications.
Sand
Almost any metal cast, no limit to size, shape or weight and low tooling costSome finishing required; somewhat coarse finish; wide tolerances
Shell Mold
Good dimensional accuracy and surface finish; high production ratePart size limited; expensive patterns and equipment required
Expandable pattern
Most metal cast with no size limit, complex shapes cast easilyPatterns have low strength and can be costly for low quantities.
Plaster Mold
Intricate shapes, good dimensional accuracy and finish, low porosityLimited to non-ferrous metals; limited size of volume and production; relatively long mold making time
Ceramic Mold
Intricate shapes, close tolerances part; good surface finishLimited size
Investment
Intricate shapes; excellent surface finish and accuracy almost any metal castPart size limited; expensive patterns, equipment and labor
Permanent mold
Good dimensional accuracy and surface finish; high production rate; low porosityHigh mold cost; limited shape and intricacy; not suitable for high melting point metals
Die
Excellent dimensional accuracy and surface finish; high production ratesHigh die cost; part size limited; usually limited to non-ferrous metals; long lead time